◆プロセス製造業におけるMRPとは?運用の流れや導入による効果を解説
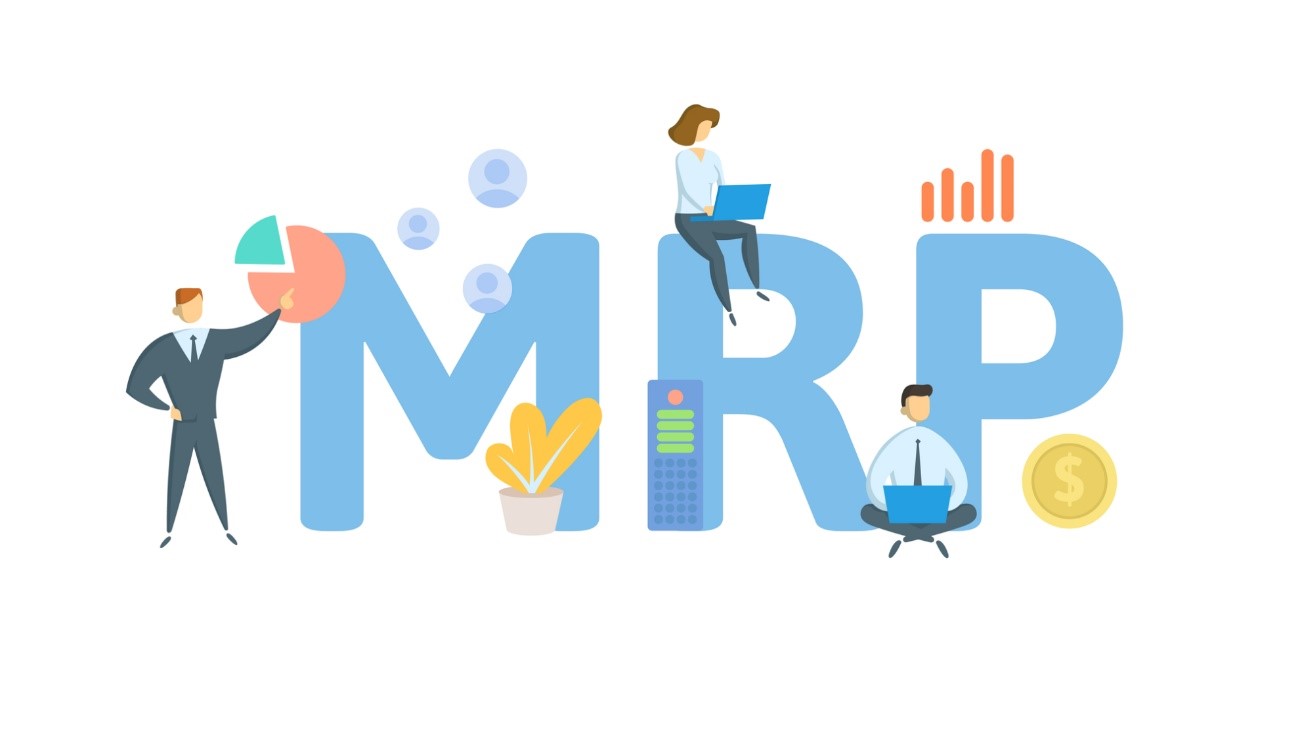
MRPとは、原料や材料などを適切に購買するための生産管理手法です。MRPでは生産計画を基に必要な原材料の発注計画を立案し、生産業務の効率化を図ることを目指します。
本記事では、医薬・化粧品・健康食品などのプロセス製造業におけるMRPの概要や運用の流れ、生産スケジューラとの違い、導入による効果や注意点を解説します。MRPの内容を詳しく知りたい方は、ぜひ参考にしてください。
MRP(Material Requirements Planning System)とは生産管理手法の一つで、日本語では「資材所要量計画」ともいいます。MRPでは、必要なものを適切なタイミングで適切な量を購買・製造するために、生産計画を基に必要となる原材料の数を計算し、いつ購入するかを決定します。
つまり、在庫管理や発注業務を効率的に行なうための手法がMRPだといえるでしょう。MRPの導入によって自社の状況を正確に把握し、原材料調達を最適化すると、在庫管理のコスト削減や生産性の向上を図ることができます。
MRPは、1970年代にアメリカ生産在庫管理協会(APICS:American Production and Inventory Control Society)により提唱されて急速に活用が広まり、現在も製造の現場で使用されています。
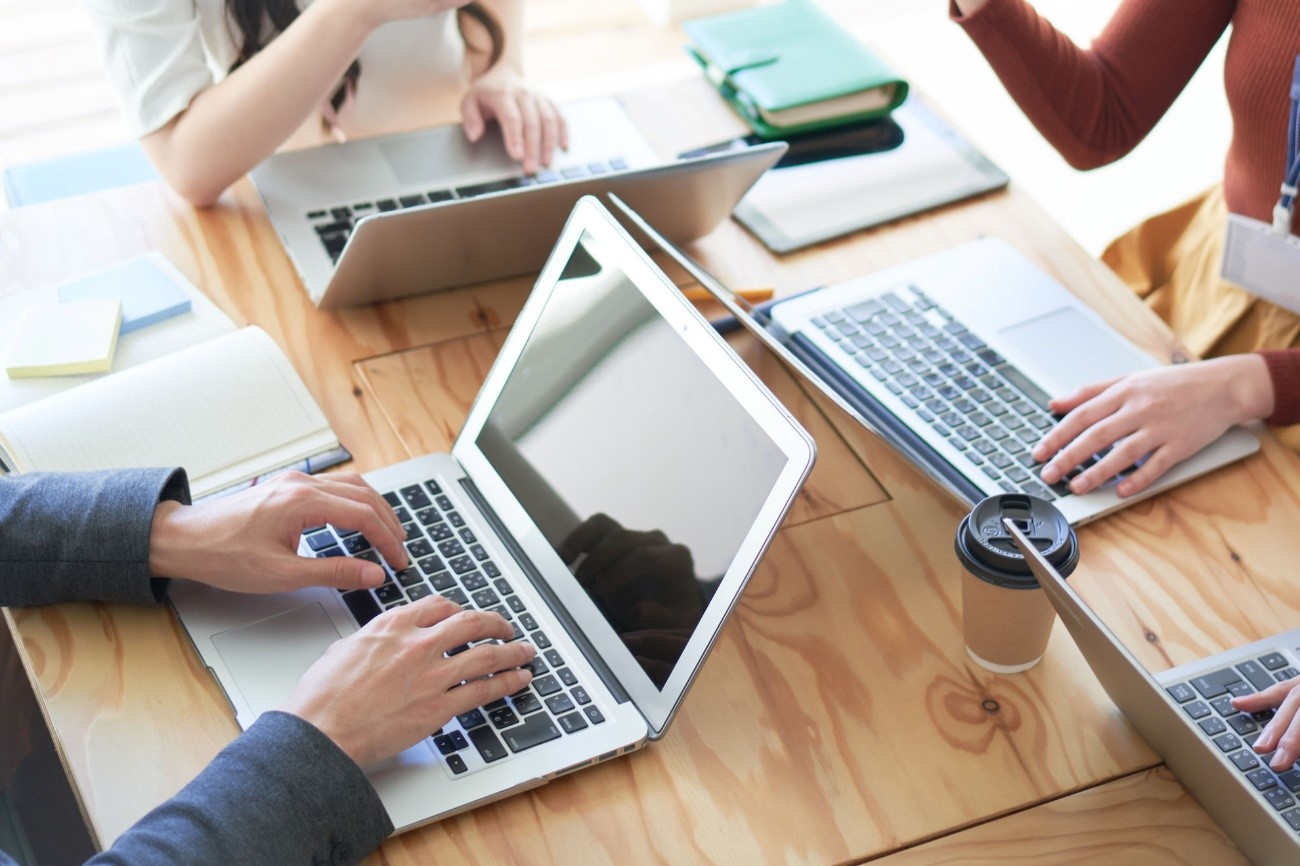
MRPを運用するためには、生産計画・配合表(部品構成表)・在庫情報の3つが必要です。ここでは、それぞれの項目についての詳細と、MRPを運用する際の一般的な流れを紹介します。
◇生産計画の立案
生産計画では、何を、どれくらいの数量、どのタイミングで生産するのかなどを決定します。計画には、製品の原材料に関する内容や、製造から出荷までのスケジュールに関する内容も含まれます。
生産計画の指示は、以下のように「押し出し方式(PUSH型)」と「引っ張り方式(PULL型)」という2パターンに分けられます。
・押し出し方式(PUSH型):事前に立案した計画をもとに作業を進める「押し込み生産」を行なうための生産計画
・引っ張り方式(PULL型):受注した数量や納期を見て、生産工程の後工程(下流側)から前工程(上流側)へ向かって製造を指示する「引き取り生産」を行なうための生産計画
MRPの生産計画の指示は押し出し方式です。生産計画を立てる際には、まず過去の受注データを参考にして需要予測を行ないます。
◇配合表(部品構成表)を基に原材料の総使用量を算出
生産計画により使用する原材料が決まると、配合表を基に総使用量を算出します。配合表は、製品の生産に必要な原材料や半製品の情報を一覧にしたもので、「BOM(Bill Of Material)」とも呼ばれます。
原材料の総使用量を算出する際、原材料の総使用量の算出は、在庫状況を考慮せず行ないます。在庫から生産に必要な原材料を調達できる場合も、材料がない状態として単純に総使用量を算出します。
◇在庫状況を考慮して原材料の正味所要量を計算
原材料の総使用量を算出したら、在庫数や発注残(発注済みで未納のものの数)などの在庫情報を確認します。
総使用量の計算では在庫を考慮しませんでしたが、正味所要量計算では在庫の差し引きを行なって適切に計算することがポイントです。算出した原材料の総使用量から、原材料などの在庫数や発注残、仕掛品などを差し引いて、原材料の発注の計画を行ないます。
なお、このように必要な原材料に対して、在庫状況を考慮して原材料の発注を行なう工程は「発注計画」とも呼ばれます。
◇購買計画
購買計画では、MRPの結果を基に発注先の選定や評価、注文単価の設定、検査予定日の決定など、具体的な調達活動を行ないます。購買計画は最近では生産管理業務の一部として、生産管理システムやERPシステムなどを活用して効率化することも少なくありません。
システムとしてのMRPは生産管理を対象としており、生産計画から必要な原材料の発注計画を立案し、生産業務の効率化を図ります。
一方で、生産スケジューラ(APS:Advanced Planning and Scheduling)は生産計画や製造スケジュールを管理する仕組みで、製造業で使われる情報システムの一つです。生産スケジューラでは使用する設備や作業時間、人員などを考慮するため、より詳細に生産計画や製造スケジュールを管理することが可能です。過去の実績や現状の人・設備といったリソースを踏まえて日々の生産スケジュールを最適化すれば、需要の変化や働き方改革による勤務時間制約などに対応できます。
なお、MRPに生産スケジューラを連携するケースもあります。生産スケジューラを使って制約を考慮した生産計画を立て、MRPで原材料調達と在庫管理の最適化を図り、生産プロセス全体のスムーズな運用の実現を目指します。
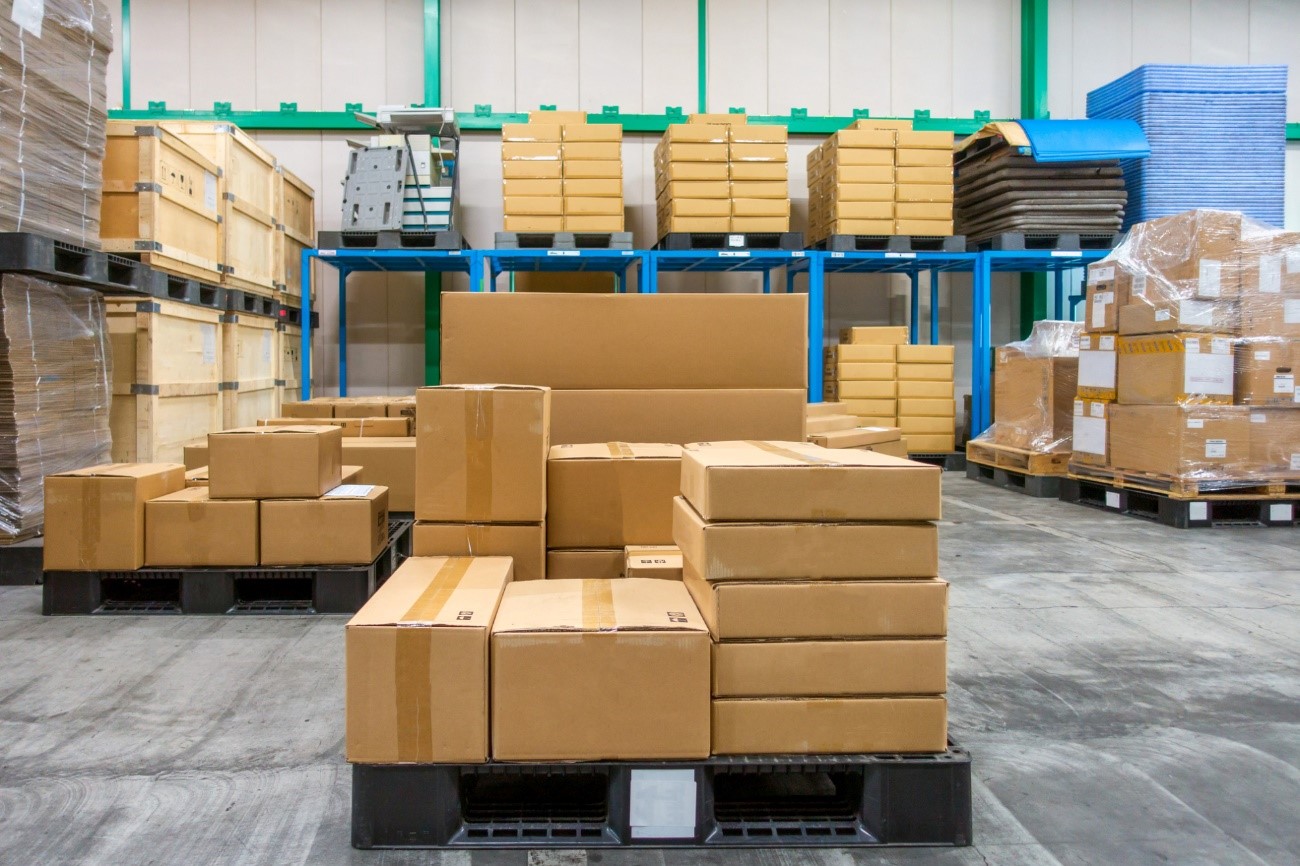
ここからは、MRPを導入することで得られるおもな効果を紹介します。
◇在庫の適切な管理
MRPの導入により、適切な在庫管理を行なえるようになります。例えば、在庫が過剰になり、長期間保管された場合、原材料の劣化が進むなどの問題が発生します。一方、在庫が不足すれば、納期の遅延の原因となり、取引先との信頼を損なうことにもなりかねません。
在庫の過不足に起因する問題発生を防ぎ、安定した生産体制を維持することができます。
◇仕入や在庫管理にかかるコストの削減
MRPを導入すれば、原材料の発注を計画的に行なえるようになり、経済的にメリットのある量で発注できることもあります。
また、在庫回転率の向上が期待できます。在庫回転率とは、一年間に何回在庫を入れ替えるかを表す指標であり、数値が高いほど、在庫を効率的に活用できているといえます。在庫回転率が上がって在庫管理が適切にできれば、在庫の保管や破棄に生じるコストを削減できます。
上記は製品原価を下げることにつながり、企業の競争力向上にも寄与するといえるでしょう。
◇業務効率化による生産性の向上
原材料の所要量を人の手のみで算出し発注するとなれば多大な時間がかかりますが、MRPを導入することで大幅な時間短縮が可能になります。さらに、システム化することで発注時の計算ミスや二重発注なども軽減でき、業務効率化や生産性の向上が期待できるでしょう。
MRPは有効なシステムですが、導入にあたっては注意すべき点もあります。以下から詳しく見ていきましょう。
◇生産計画や配合表(部品構成表)、登録するシステムデータなどの精度により結果が左右される
MRPでは生産計画や配合表、在庫情報などのデータに基づいて原材料の所要量を算出します。そのため、もとになるデータの精度が低ければ、算出される所要量の精度もその分低くなってしまいます
例えば、配合表の粒度が十分でなかったり、マスタデータが見直されていなかったりするとデータの精度が低いため、スムーズに運用できない可能性があります。
プロセス製造業においてMRPを行なうには、生産計画や品質管理(GMP、ロットトレース)、購買管理、在庫管理などの機能も合わせて必要です。
JIPROSは、中堅プロセス製造業のために開発された統合管理(販売・生産・原価)パッケージで、MRPを含む生産管理システムです。
医薬品、化粧品、健康食品製造業への生産管理システムの導入には、業界のノウハウ、GMP規制対応支援、ハードウエアサポートなどが欠かせません。JIPROSは日本電子計算株式会社によってワンストップ導入を行なっているため、初めて生産管理システムを導入する場合でも安心して導入いただけます。
導入ノウハウや業界知識を活用し、導入から運用まで、すべてを手厚くサポートいたします。
MRP(資材所要量計画)は、在庫管理や発注業務を効率化する生産管理手法の一つです。購買や製造を適切に行なうために、生産計画に基づいて原材料の所要量を算出し、購入時期を決めます。また、MRPができるシステムもあります。
一方、生産スケジューラ(APS)は製造業で使われる情報システムの一つで、生産計画や製造スケジュールを管理するものです。リソースや生産能力の制約を考慮した生産計画を立案できるのが特徴で、MRPと連携して利用するケースもあります。
MRPを導入すれば在庫の適切な管理が可能になり、仕入や在庫管理にかかるコストも削減できるなど、高い効果が見込めます。また、業務効率化による生産性の向上も期待できるでしょう。導入にあたっては、生産計画や配合表(部品構成表)、登録するシステムデータの精度により結果が左右される点に注意が必要です。
医薬・化粧品・健康食品などのプロセス製造業においてMRPの導入を検討している方は、JIPROSの導入を、ぜひご検討ください。